Heavy Industrial Processing
If your processes involve extreme temperature, abrasive materials or corrosive products, Blasch has the solution to extend the life, reduce downtime and improve your bottom line. Blasch works with designers and engineers to replace existing metallic components, machined silicon carbide elements or monolithic structures with our pre-cast silicon carbide shapes and reducing operational costs.
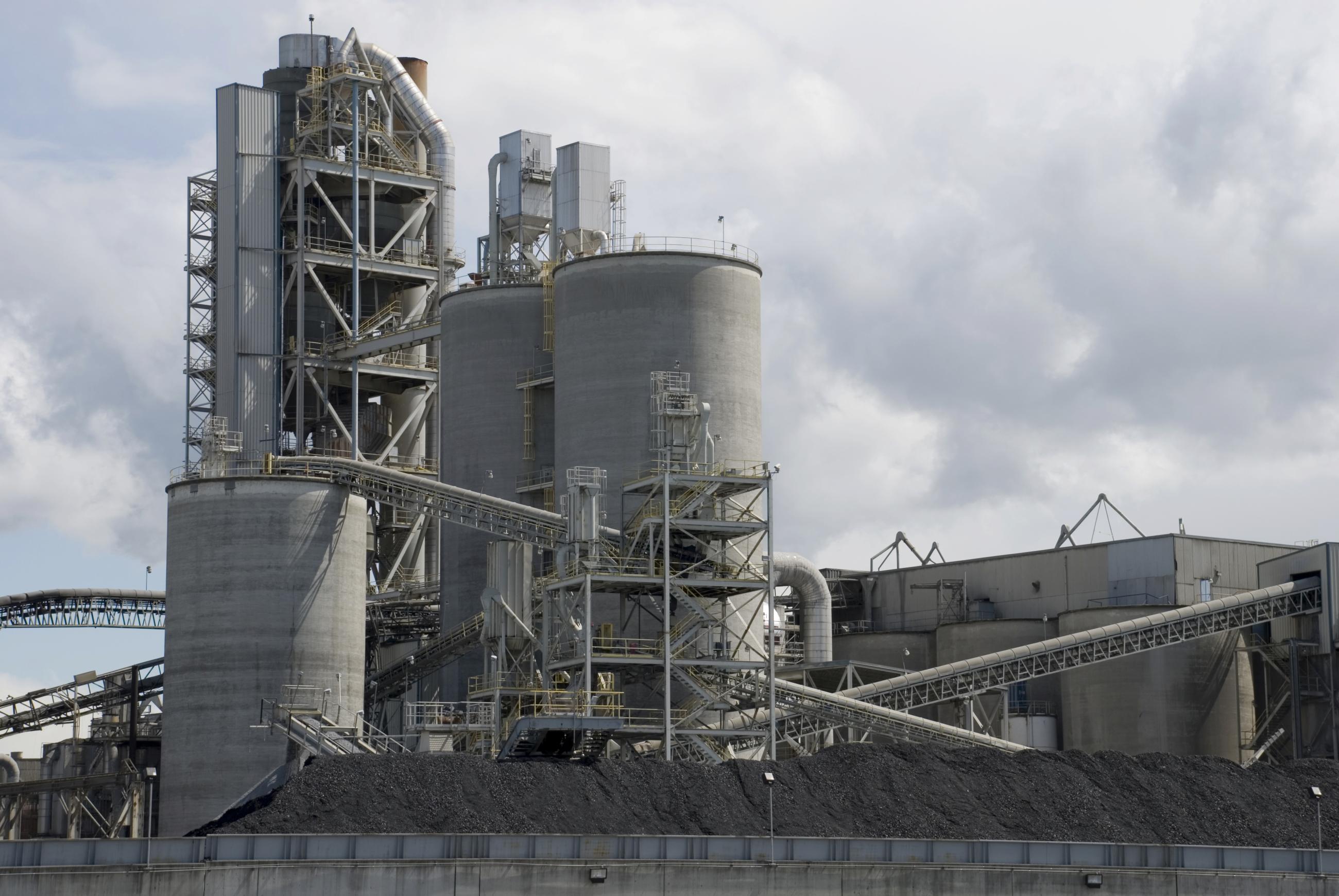
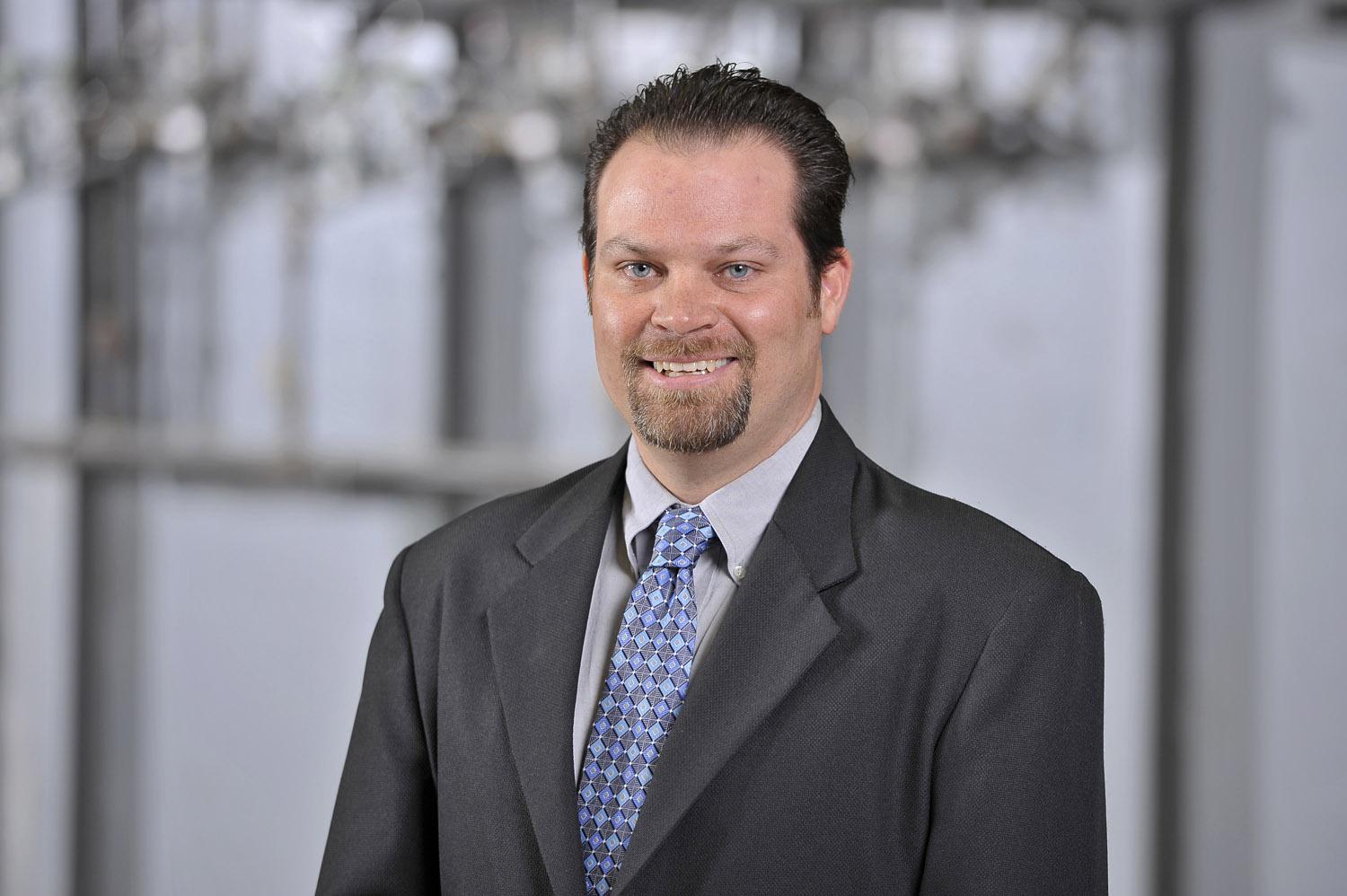
MARKET MANAGER
Tim Connors, Director of Business Development, Blasch Global Solutions
+1-518-436-1263 Ext. 105
Tim Connors, Senior Market Manager, has been with Blasch Precision Ceramics since 1995. He holds a Master of Science degree in Advanced Technology. A Mechanical Engineer by education, he has configured abrasion resistant solutions, molten metal linings, flow control systems, high temperature firing fixtures and chemical and corrosion lining systems using Blasch’s unique forming method and custom materials. His area of expertise is in custom wear applications for the Power Generation, Mining, Industrial Process Heating and Heavy Industrial Processing industries. He currently manages the Energy & Chemical Markets, which include Refining/Chemical Processing, Mining, Heavy Industrial Processing, Industrial Process Heating and Power Generation. In addition to that he holds a role in Business Development for our Global Specialty Products division.
Cement Production
Blasch has extensive global experience in solving every day challenges of modern cement production, particularly in the dry calcining process, often pioneering new high temperature abrasion resistant solutions, such as Altron ™, Oxytron™ and Nitron™ silicon carbide designed to improve plant efficiency, reliability and environmental performance. Blasch offers advance silicon carbide solutions for wear and structural applications that often replace a metallic piece. Alkali and abrasion resistant high performance Oxytron and Nitron silicon carbide clinker cooler wear inserts and grates, multicyclone dust collectors, pipe liners, valves, dip tube/thimbles and other shapes are available. Custom precision silicon carbide shapes and systems are available for any area of the plant that is seeing abrasion, high temperature or corrosive duty.
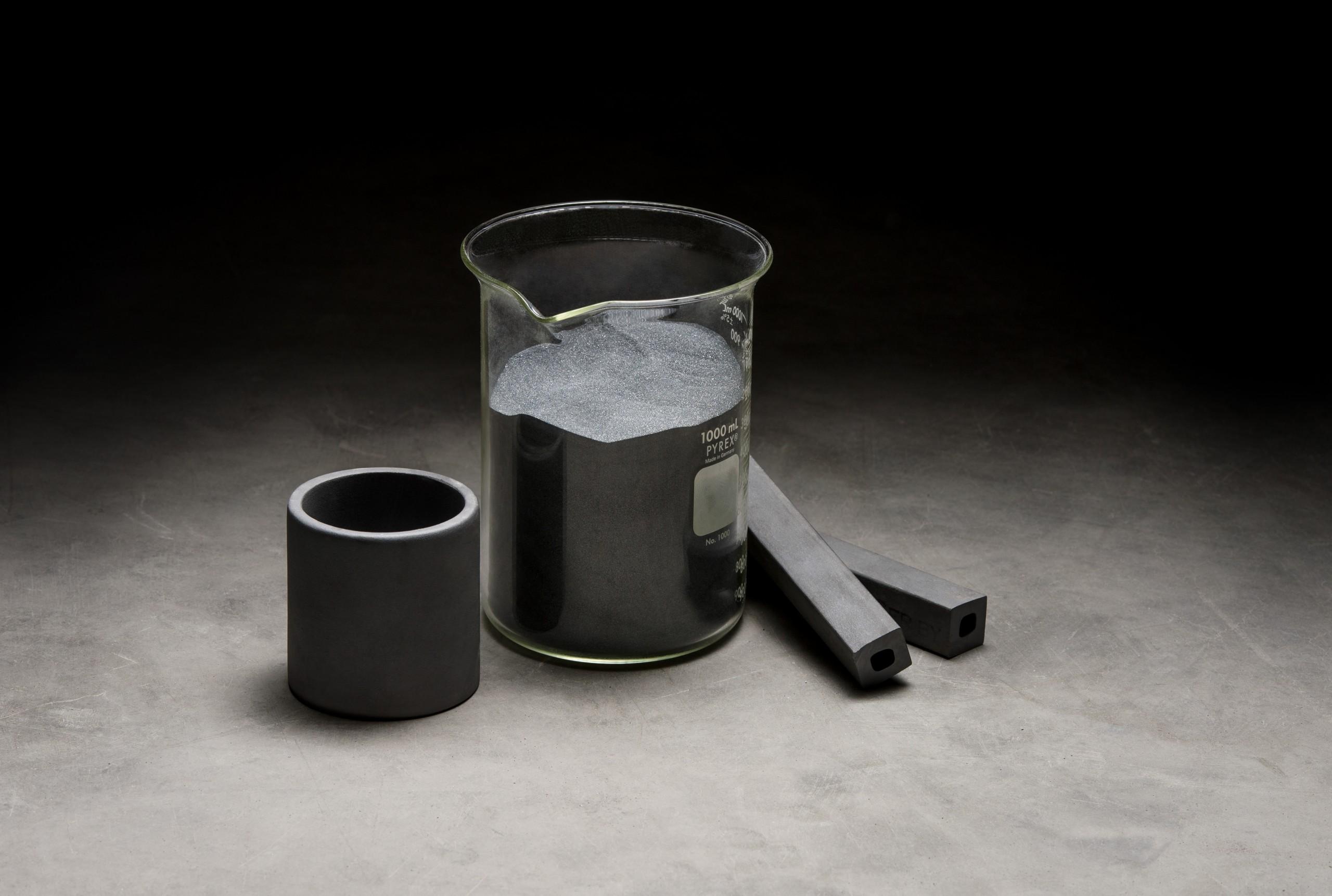
TiO2 Production
Blasch has extensive global experience in solving every day challenges of modern TiO2 production, particularly in the finishing process, often pioneering new high temperature abrasion and corrosion resistant solutions. Blasch Altron ™, Oxytron™ and Nitron™ silicon carbide were designed to improve plant efficiency, reliability and environmental performance. Blasch offers advanced silicon carbide solutions for wear and structural applications that often replace a metallic piece. Wear resistant micronizer linings, hot tickle piping, valves, reactor linings, chlorinator parts and other shapes are available.
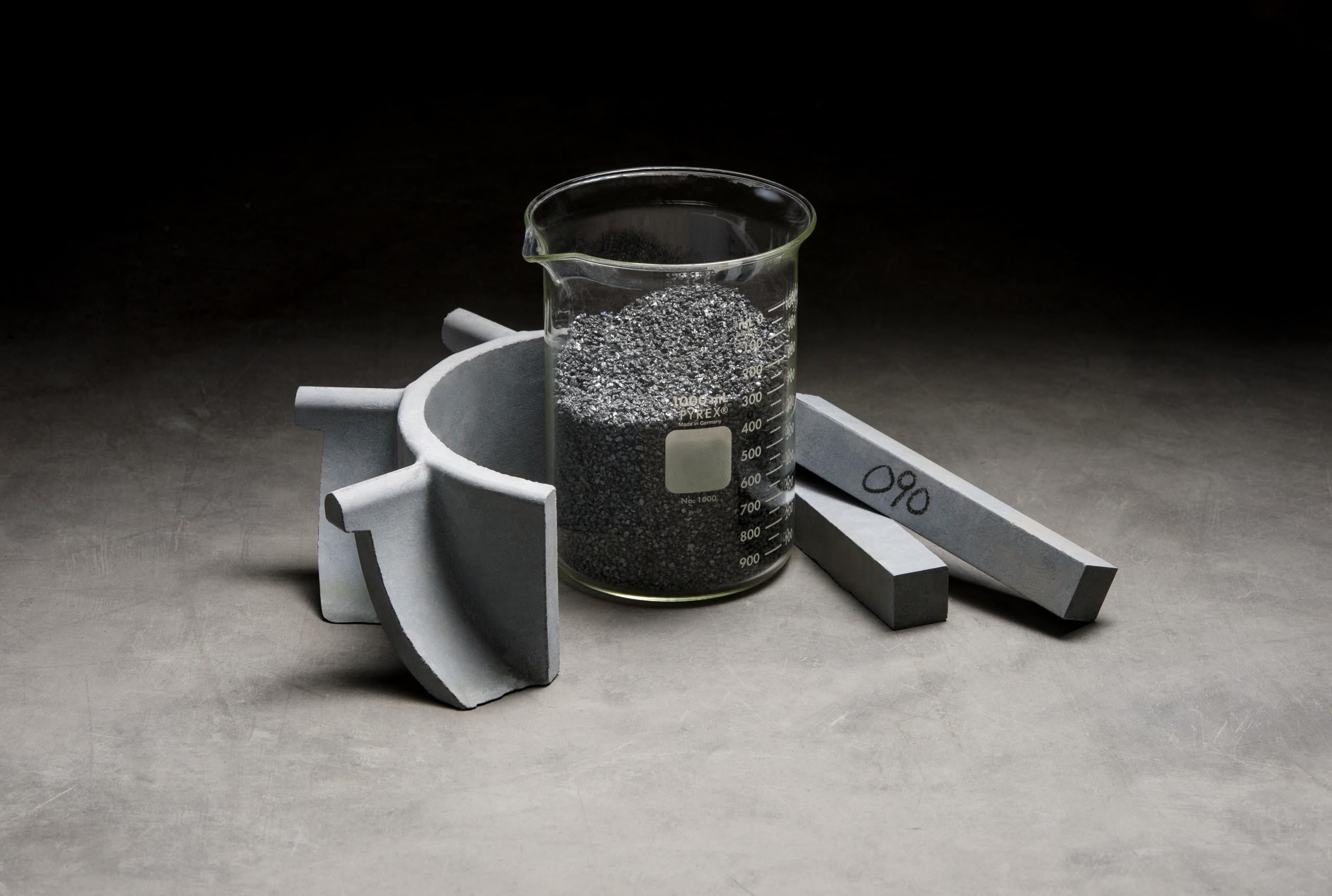
Iron Ore Pelletizing
Blasch has extensive global experience in solving every day challenges of the modern Iron Ore Pelletizing process, particularly in the kiln process, often pioneering new high temperature abrasion and corrosion resistant solutions, such as Altron ™, Oxytron™ and Nitron™ silicon carbide designed to improve plant efficiency, reliability and environmental performance. Blasch offers advanced silicon carbide solutions for wear and structural applications that often replace a metallic piece. Wear resistant dust collectors, piping, valves, reactor linings and other shapes are available.
Pet Coke
Blasch has extensive global experience in solving every day challenges of modern Pet Coke and Carbon Black production, often pioneering new high temperature abrasion and corrosion resistant solutions, such as Altron ™, Oxytron™ and Nitron™ silicon carbide designed to improve plant efficiency, reliability and environmental performance. Blasch offers advanced silicon carbide solutions for wear and structural applications that often replace a metallic piece.
Glass Production
Blasch has extensive global experience in solving every day challenges of modern Pet Coke and Carbon Black production, often pioneering new high temperature abrasion and corrosion resistant solutions, such as Altron™, Oxytron™ and Nitron™ silicon carbide designed to improve plant efficiency, reliability and environmental performance. Blasch offers advanced silicon carbide solutions for wear and structural applications that often replace a metallic piece.
Building Materials Manufacturing
Blasch has extensive global experience in working with companies that supply building materials. Be it bricks, concrete, or even solar panels, we have pioneered new high temperature abrasion and corrosion resistant solutions, such as Altron ™, Oxytron™ and Nitron™ silicon carbide designed to improve plant efficiency, reliability and environmental performance. Blasch offers advanced silicon carbide solutions for wear and structural applications that often replace a metallic piece. Wear resistant brick extrusion cores, valves, kiln furniture, lining systems, ceramic lined pipe, and other shapes are available.
Wireline Industry
Blasch has extensive global experience in solving every day challenges of modern wire production, particularly in the heat treating and galvanizing process, often pioneering new high temperature abrasion and corrosion resistant solutions, such as Altron™, Oxytron™ and Nitron™ silicon carbide designed to improve plant efficiency, reliability and environmental performance. Blasch offers advanced silicon carbide solutions for high temperature, wear and structural applications that often replace a metallic piece. Wear resistant weir bars, wipe stones, rollers and guides; along with immersion heater tubes, burner systems and other shapes are available.
Silicon Production
Furnace Engineers worldwide rely on Blasch high performance silicon carbide and alumina components. Custom engineered reactor vessel linings and other shapes, along with engineered materials replace traditional monolithic refractories. Blasch designs and high purity advanced materials like alumina and silicon carbide allow engineers to maximize process capacity by engineering ceramic around the customer’s process. Once installed, Blasch’s high strength thermal shock resistant compositions make it easier for the plant to achieve financial performance objectives by optimizing throughput while reducing the fuel consumption and need for costly maintenance/replacement of existing structures.