Industrial Process Heating
For more than three decades, Blasch has worked with designers and engineers to replace existing metallic components, thick castable parts or machined ceramic elements with our pre-cast high purity alumina and silicon carbide shapes – saving money and reducing downtime. Low mass kiln furniture, thin walled burner tiles and other complex shapes are made with superior materials and cast with precision for repeatable, long life.
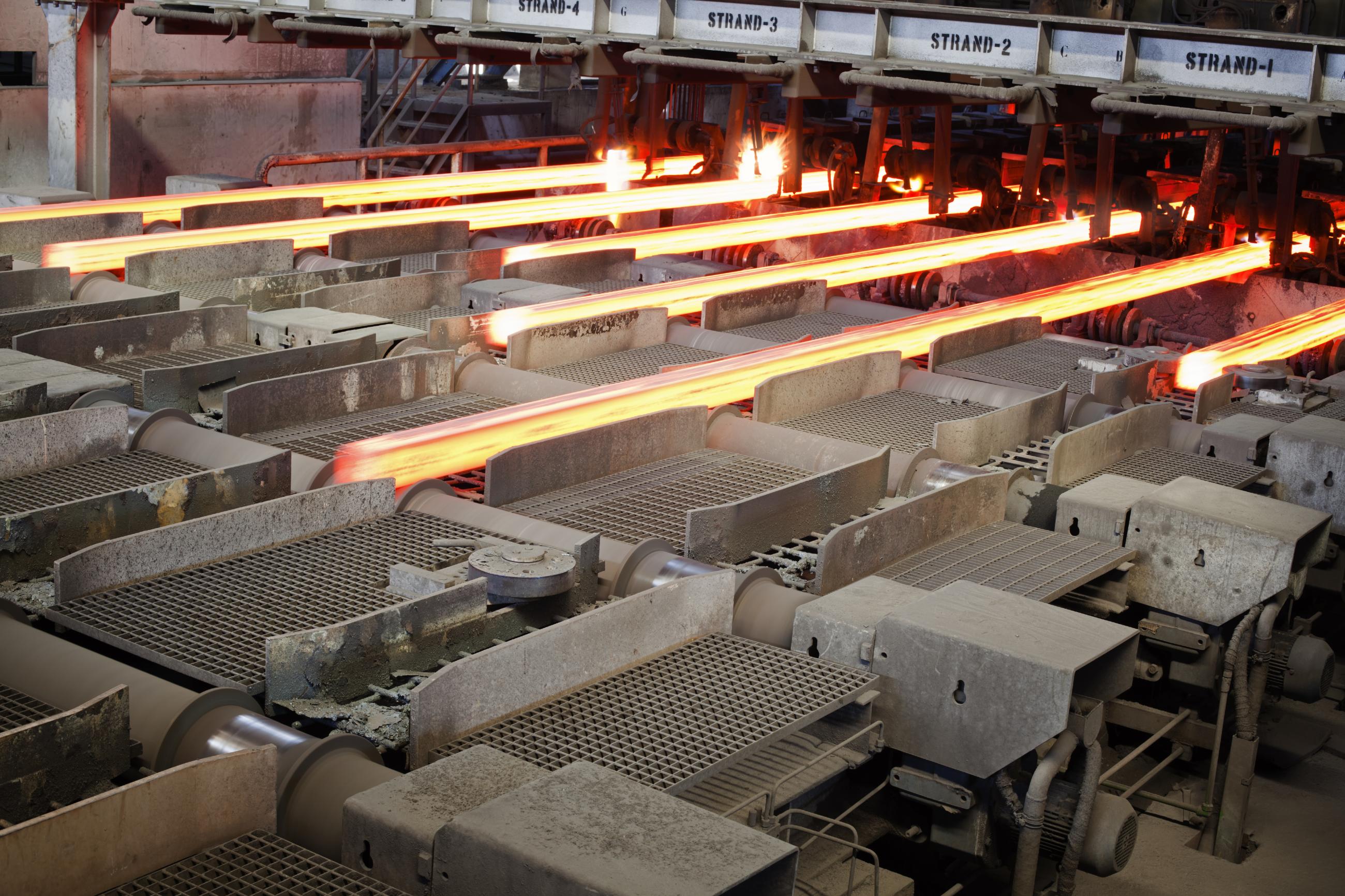
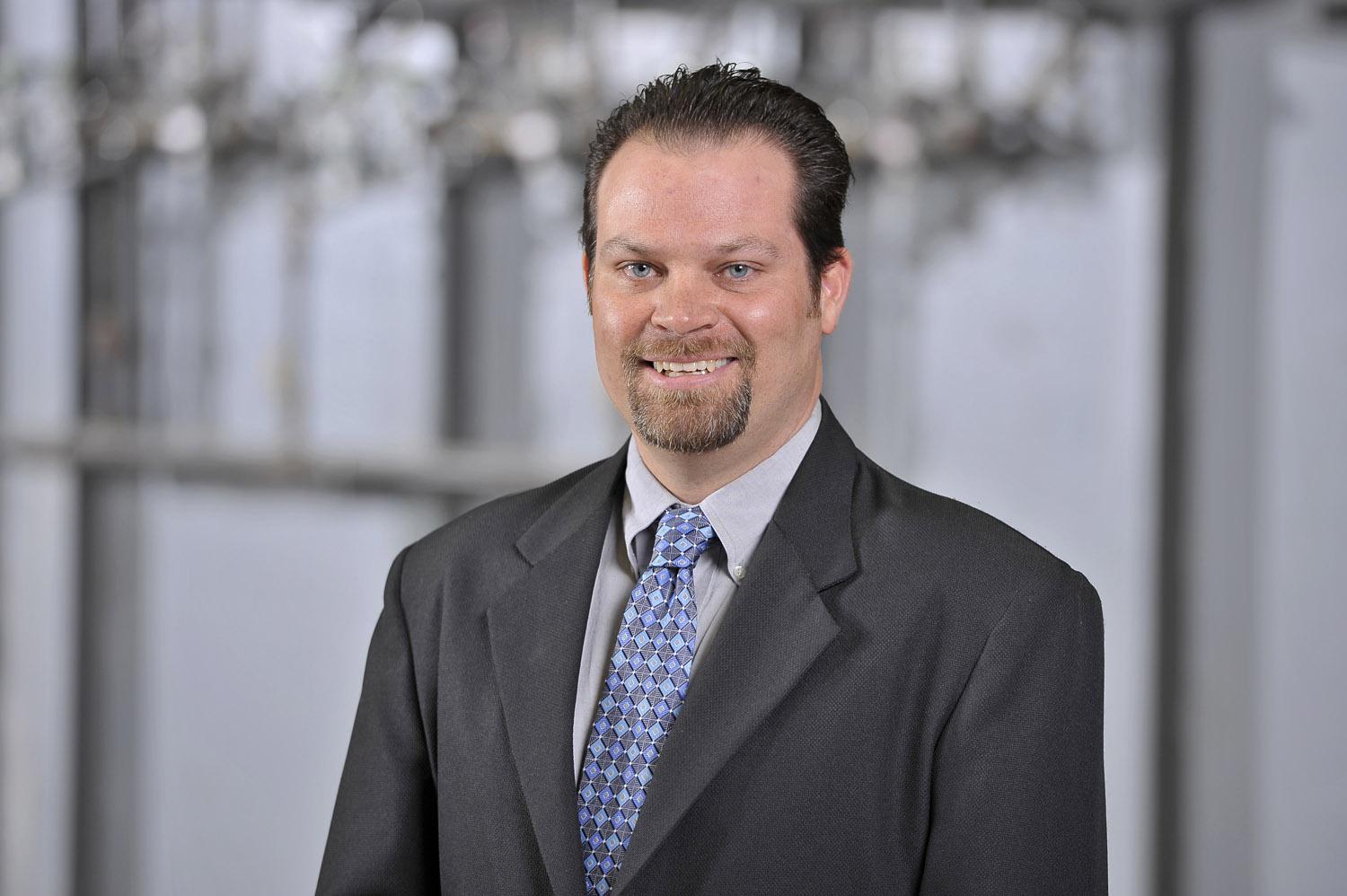
MARKET MANAGER
Tim Connors, Director of Business Development, Blasch Global Solutions
+1-518-436-1263 Ext. 105
Tim Connors, Senior Market Manager, has been with Blasch Precision Ceramics since 1995. He holds a Master of Science degree in Advanced Technology. A Mechanical Engineer by education, he has configured abrasion resistant solutions, molten metal linings, flow control systems, high temperature firing fixtures and chemical and corrosion lining systems using Blasch’s unique forming method and custom materials. His area of expertise is in custom wear applications for the Power Generation, Mining, Industrial Process Heating and Heavy Industrial Processing industries. He currently manages the Energy & Chemical Markets, which include Refining/Chemical Processing, Mining, Heavy Industrial Processing, Industrial Process Heating and Power Generation. In addition to that he holds a role in Business Development for our Global Specialty Products division.
Sintering, Firing, Calcining, Annealing, Heat Treating
Kiln room operators and Furnace Engineers rely on Blasch high performance kiln furniture components. Custom engineered low mass structural support assemblies replace traditional cast block and thick plate arrangements. Blasch designs high purity advanced materials like alumina and silicon carbide allowing kiln room operators to maximize firing capacity by engineering kiln furniture around the customer’s ware.
Once installed Blasch’s high strength thermal shock resistant compositions make it easier for the plant to achieve financial performance objectives by optimizing kiln throughput while reducing the fuel consumption and need for costly maintenance/replacement of existing support structures.
Furnaces
Furnace Engineers and plant operators worldwide come to Blasch when they have a maintenance or process problem in their furnaces. After employing thick, bulky monolithic refractory or brick structures to solve their insulation issues, they search for a better solution.
Blasch’s high performance engineered insulating shapes, element holders, and burner components are made in high strength and thermal shock resistant material that can be cast into intricate and precise shapes for ease of installation and repeatability. Once installed the furnace can operate as expected with minimal downtime and without costly repairs. Learn more about our ceramic solutions for Industrial Process Heating applications.
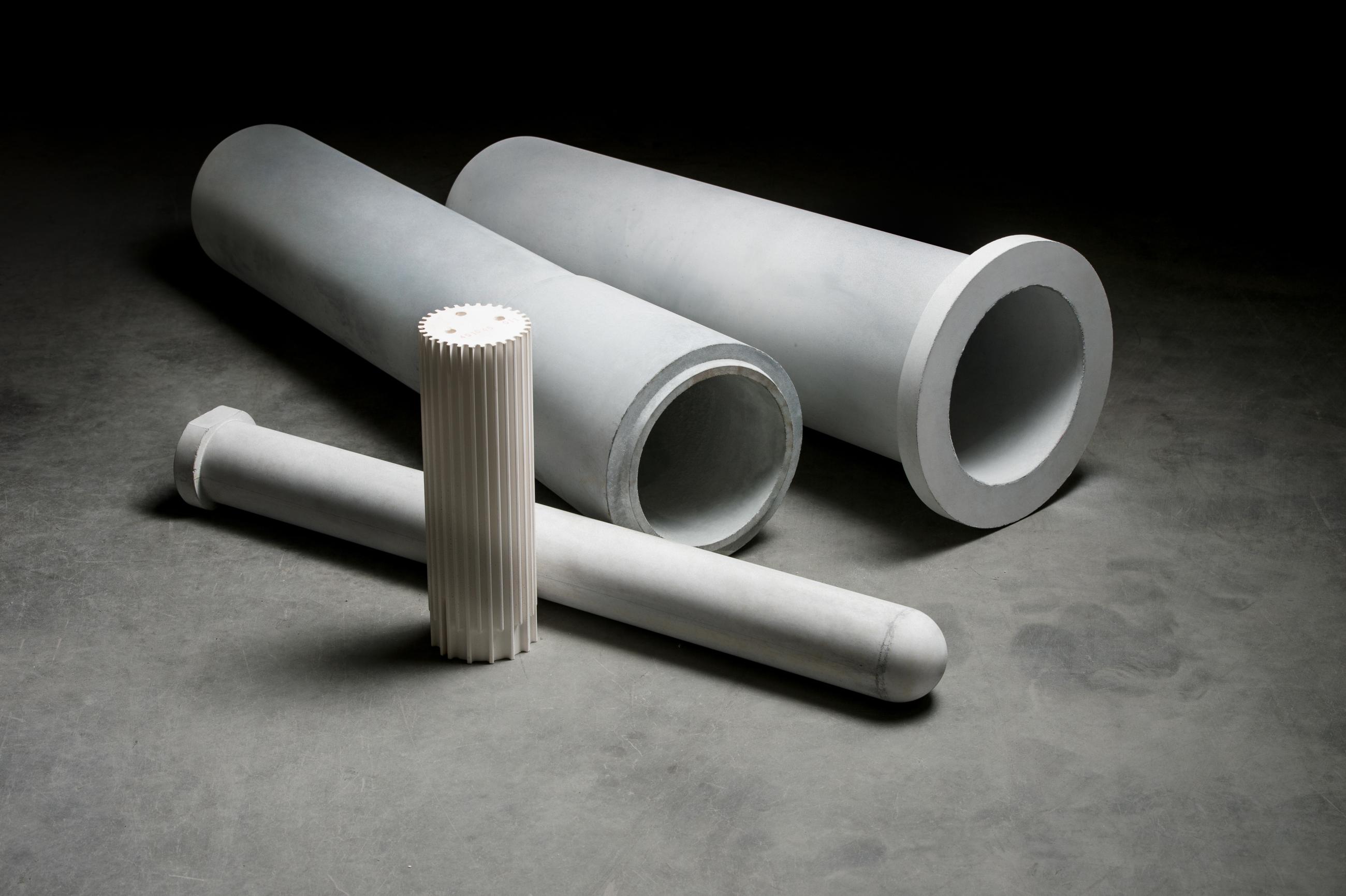
Semiconductor
System Engineers rely on Blasch high performance, high purity components that support and transport semiconductor products like wafers and chips through thermal processing. Custom engineered low mass structural support assemblies replace traditional graphitic or quartz arrangements in horizontal or vertical furnaces.
Blasch designs high purity advanced materials like CVD coated alumina and silicon carbide which allow furnace operators to maximize diffusion capacity by engineering kiln furniture around the customer’s ware and needs.