
Dust Collector Components - Mechanical
Maintenance managers and engineers worldwide rely on Blasch high-performance OXYTRON™ and ALTRON™ silicon carbide SiClone™ mechanical dust collector components. Because they are engineered to replace existing steel components or liners, Blasch SiC dust collectors give maintenance managers freedom to worry about other parts of their plant. Blasch’s abrasion-resistant silicon carbide composition far outlasts traditional cast iron or Ni-Hard by orders of magnitude. As a result, it is easier for plant operators to achieve financial performance objectives by optimizing separation efficiencies, maximizing cyclone life, and eliminating maintenance/replacement costs traditionally found with metallic components.
APPLICATIONS FOR MECHANICAL DUST COLLECTOR COMPONENTS
- Power plants and industrial boilers (coal, biomass, bagasse, wood, hog fuel)
- Pulp and paper
- Cement plants (clinker dust)
- Steel and iron ore pelletizing plants
- Mining and milling
- Coke processing
- Materials handling
- Brick manufacturing
- Palm oil extraction
One of the biggest costs incurred in the operation of a plant is the maintenance and repair of the dust collection system. Due to the attack of particles at low acute angles of impingement, a mechanical dust collector faces extreme abrasive wear. However, engineering and shape-making capabilities unique to the Blasch process allow for pre-cast refractory multicyclone parts with superior abrasive resistance. Blasch components are made of silicon carbide and come with engineered mounting rings for structural reliability and ease of installation.
Blasch multicyclone dust collectors are 38% the weight of comparable iron components, making them easier to install, and are available in all sizes and all designs. These pieces of equipment are instrumental in removing large particulate from a high temperature process gas stream. With the OXYTRONTM material we employ in these components, they far exceed the life by 10x over the cast steel products that are often prone to developing holes during their life cycle. These holes ultimately allow the particulate to bypass the process leading to increased emissions.
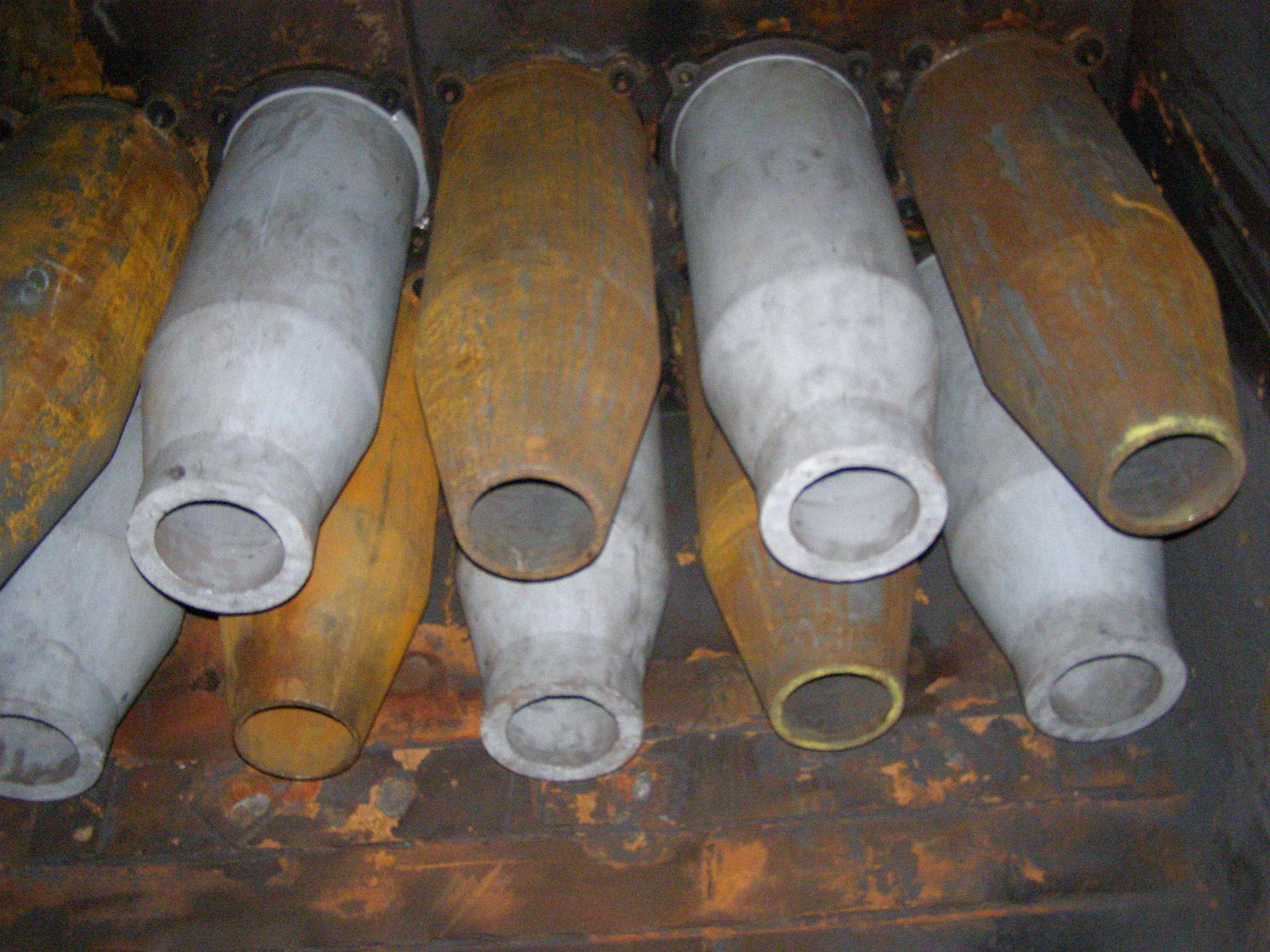
For more information or to receive a quote for these products, contact us today.
With the aid of the Blasch casting process, recent changes in geometry have resulted in a new generation of ultra-high efficient multi cyclones. The surface of a typical cast iron cone is quite rough with some irregularities. In contrast, the Blasch ceramic multicyclone surface is extremely smooth due to our patented and precise casting process. In addition, dimensional accuracy and geometric tolerances like roundness far exceed traditional metallic castings. This results in a dust collector assembly that is more efficient than metal or cast iron.
One of Blasch’s largest SiCloneTM dust collectors got installed at a biomass-fired plant in 2017. As of Spring 2020, the ceramic is holding very up well and the plant is well pleased with the labor and cost savings of switching to ceramic. View some photos from this 24-inch SiClone installation.
Product Information Sheets
RELATED RESOURCES
All-round Ceramic Protection
Erosion can significantly reduce the operational life of cement production equipment and speed up the replacement of key components. The use of abrasion-resistant precast ceramic parts can be a sound alternative to expensive metallic shapes or cast refractory.