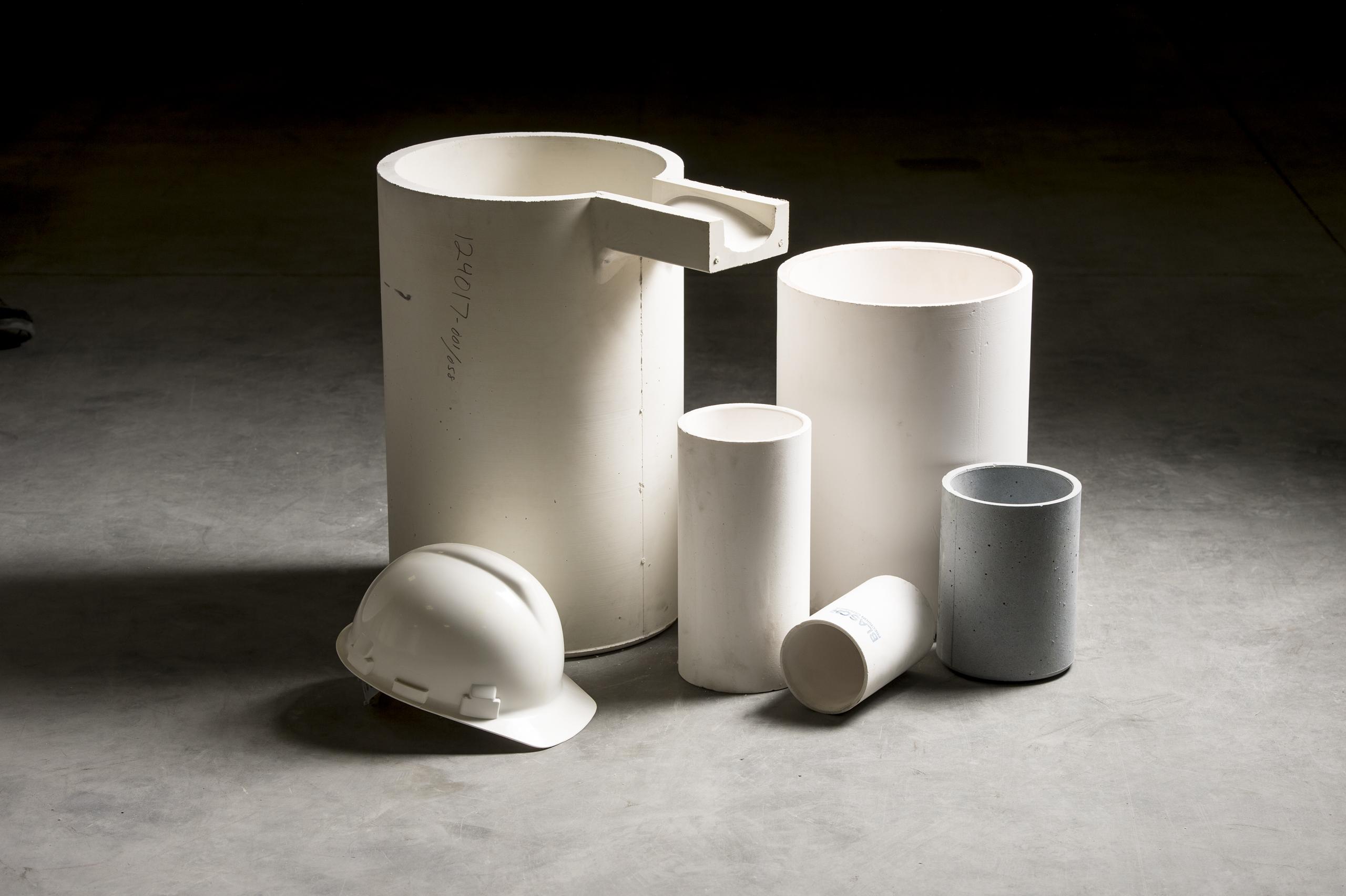
Ceramic Crucibles: High-Performance ProCaster™
Investment casters worldwide rely on Blasch high-performance ProCaster ceramic crucibles specifically engineered for coreless induction furnaces up to 5,000-pound capacity.
With crucibles available in a variety of compositions, Blasch engineers assist casters in achieving financial performance objectives.
Improve Profitability
Unreliable crucible performance increases costs through frequent change-outs and contamination-related scrap and rework. Foundries trust Blasch ProCaster high alumina crucibles for consistent, high-quality performance, enabling longer campaigns and reduced quality issues. They offer a cost-effective alternative to zirconia crucibles with equal or better results.
Reline Furnaces Faster
Blasch ProCaster host crucible system features precision casting for a tight fit and quick changeovers. Ideal for high-volume casting in air or vacuum induction melting, it enables fast furnace refining without reramming. Simplifying alloy changes and furnace campaigns, it enhances efficiency and productivity.
The Cleanest Pour Possible
Blasch ProCaster bottom pour crucible systems enable slag-reduced pouring with a precision-mated crucible, nozzle, and actuated stopper rod. Our tight tolerance ceramics ensure accurate metering and reliable performance, pour after pour, in induction furnace configurations.
For more information or to receive a quote for these products, contact us today.
With Blasch ceramic crucibles you can expect:
- Optimized metal purity
- Maximized campaign life
- Elimination of non-metallic casting inclusions
Foundries count on premium quality Blasch ProCaster™ high alumina crucibles to perform the same each and every campaign allowing them to extend campaigns and reduce downstream quality issues resulting in lower scrap and rework costs.
Blasch also offers a host / liner multi-use system and bottom pour configurations which provide unique solutions for investment casters.
Blasch ProCaster™ bottom pour crucible systems allow slag reduced pouring. By combining a crucible, nozzle, and an actuated stopper rod configuration, Blasch can create a precision mated system to provide accurate bottom pouring from an induction furnace configuration. Utilizing the precision tolerance capability that Blasch ceramic can provide, allows nozzle and rod mating surfaces that accurately meter, and perform for pour after pour.
In addition to the investment casting industry, Blasch also supplies melt crucibles for many other industries and applications including air melt casting, iron auto pour casting, dental casting crucibles, centrifugal casting, labware crucibles, glass melting, and precious metals, pour cups, one-shot liners, and various other shapes. Ramming materials are also available including spouts and extensions, back up ram, plastic capping, clamping systems, and features like cast in leak detector holes and lifting features.
Blasch offers four high alumina crucible materials tailored for optimal foundry performance:
ProCaster 043: Industry-standard high-performance alumina crucible.
ProCaster 074: Designed for alloys with high purity requirements, like sputtering target alloys.
ProCaster 086: Optimized for crack-free melting at high power levels.
ProCaster 087: Alumina-zirconia composite for superior corrosion resistance.
In this short video, Phil Geers, Blasch Senior Market Manager-Molten Metals, provides an overview of the Blasch ProCaster High-Performance Ceramic Crucibles. With these crucibles, learn how plants can expect to experience:
- Optimized metal purity
- Maximized campaign life
- Reduced ceramic inclusions