Mining
Whether you are operating a mine, processing plant or servicing the mining industry, Blasch can help you engineer the working components exposed to abrasion, high temperature or corrosion. Blasch works with designers and engineers to replace existing materials or monolithic structures with pre-engineered silicon carbide shapes, reducing costs and driving down the cost of raw materials.
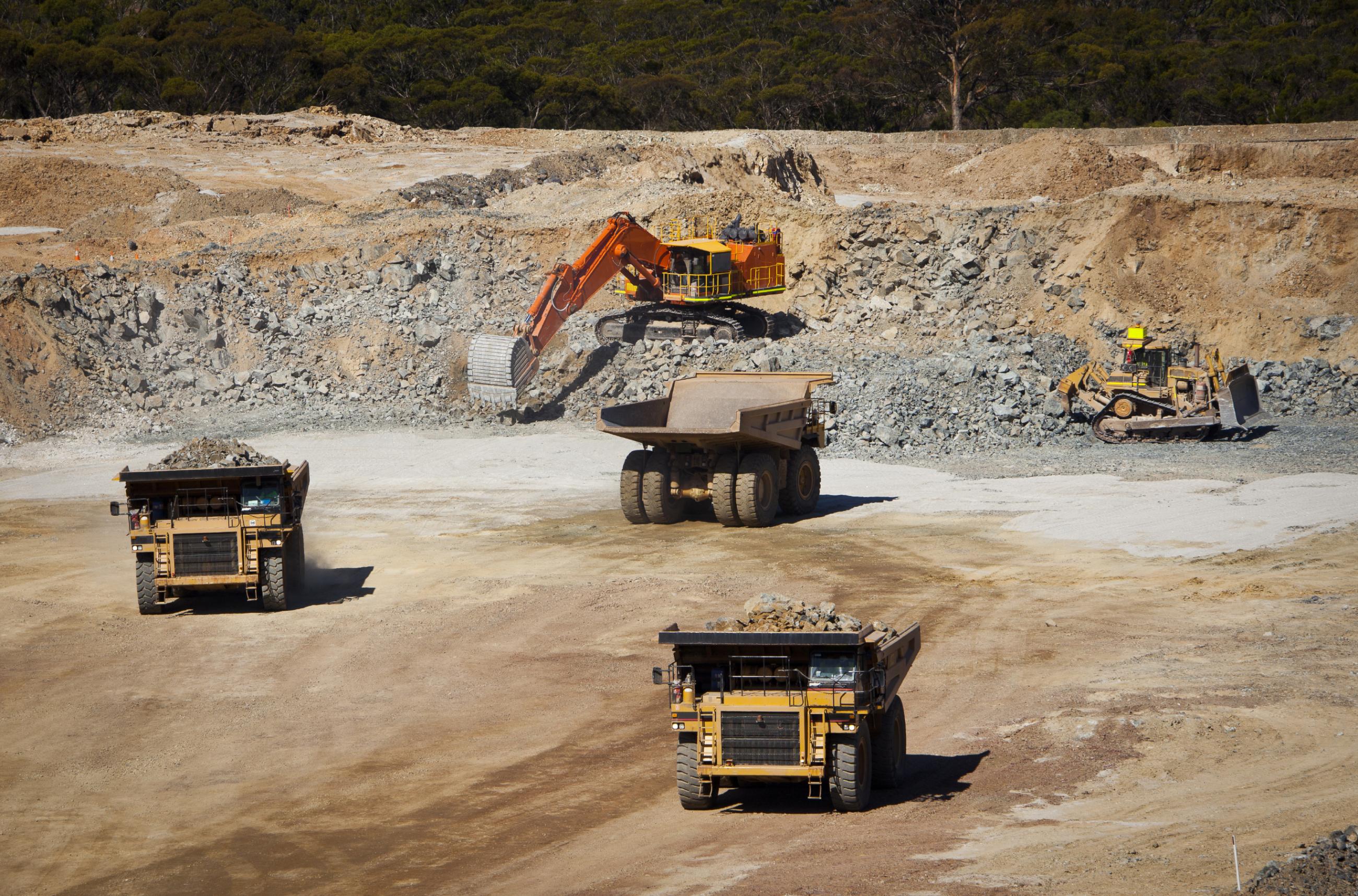
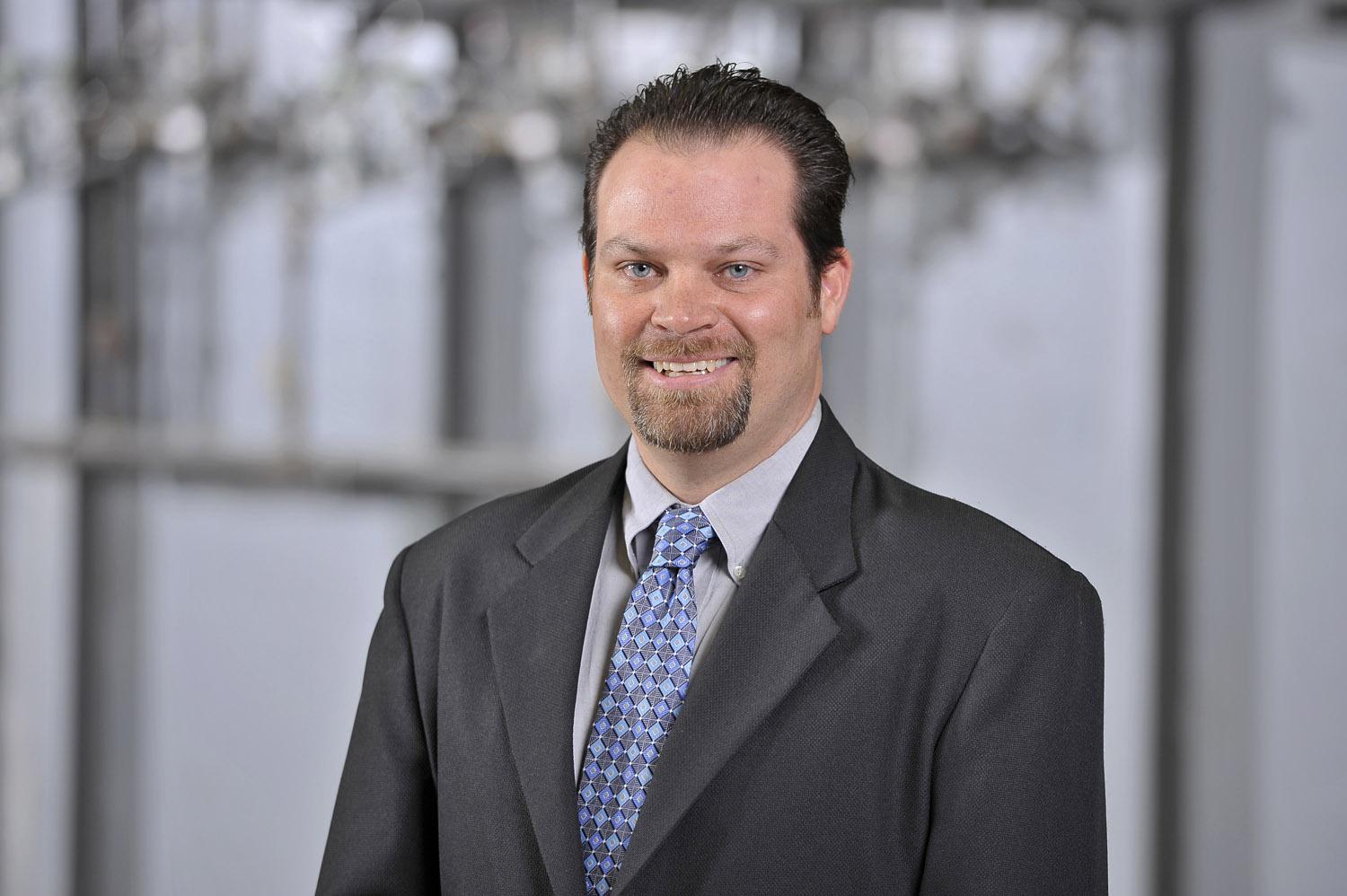
MARKET MANAGER
Tim Connors, Director of Business Development, Blasch Global Solutions
+1-518-436-1263 Ext. 105
Tim Connors, Senior Market Manager, has been with Blasch Precision Ceramics since 1995. He holds a Master of Science degree in Advanced Technology. A Mechanical Engineer by education, he has configured abrasion resistant solutions, molten metal linings, flow control systems, high temperature firing fixtures and chemical and corrosion lining systems using Blasch’s unique forming method and custom materials. His area of expertise is in custom wear applications for the Power Generation, Mining, Industrial Process Heating and Heavy Industrial Processing industries. He currently manages the Energy & Chemical Markets, which include Refining/Chemical Processing, Mining, Heavy Industrial Processing, Industrial Process Heating and Power Generation. In addition to that he holds a role in Business Development for our Global Specialty Products division.
Classifying, Separation, Mixing
Mines worldwide rely on Blasch high performance Altron™, Nitron™ and Invincer by Blasch™ monolithic drop-in replaceable silicon carbide liners specifically engineered for classifying applications in sizes up to 60 inch diameter. Liners are designed for highly abrasive ores processed such as coal, iron ore, gold, copper, cement, FGD and phosphate mining. With a variety of highly abrasion resistant compositions available, Blasch engineers assist both OEM’s and single mines in achieving financial performance objectives by optimizing classification efficiencies, maximizing cyclone life and eliminating costly installation costs traditionally found in epoxied tile constructions.
Hydro Metallurgy
World class autoclave and pressure oxidation developers continue to push the envelope in scale and process conditions. They appreciate the limitless size and shape capability that Blasch can offer. This gives them the freedom to engineer very complex, Nitron™ high temperature, abrasion and corrosion resistant lining systems for items like silicon carbide Flash Pots, Quench Vessels, Choke Tubes, Vent Blast Tubes, Impingement Blocks, Oxygen Injection Nozzles, and Pipe and Valve systems.
Pyro Metallurgy
World class autoclave and pressure oxidation developers continue to push the envelope in scale and process conditions. They appreciate the limitless size and shape capability that Blasch can offer. This gives them the freedom to engineer very complex, Nitron™ high temperature, abrasion and corrosion resistant lining systems for items like silicon carbide Flash Pots, Quench Vessels, Choke Tubes, Vent Blast Tubes, Impingement Blocks, Oxygen Injection Nozzles, and Pipe and Valve systems.